Это не столько энергетическая революция, сколько материальный драйв...
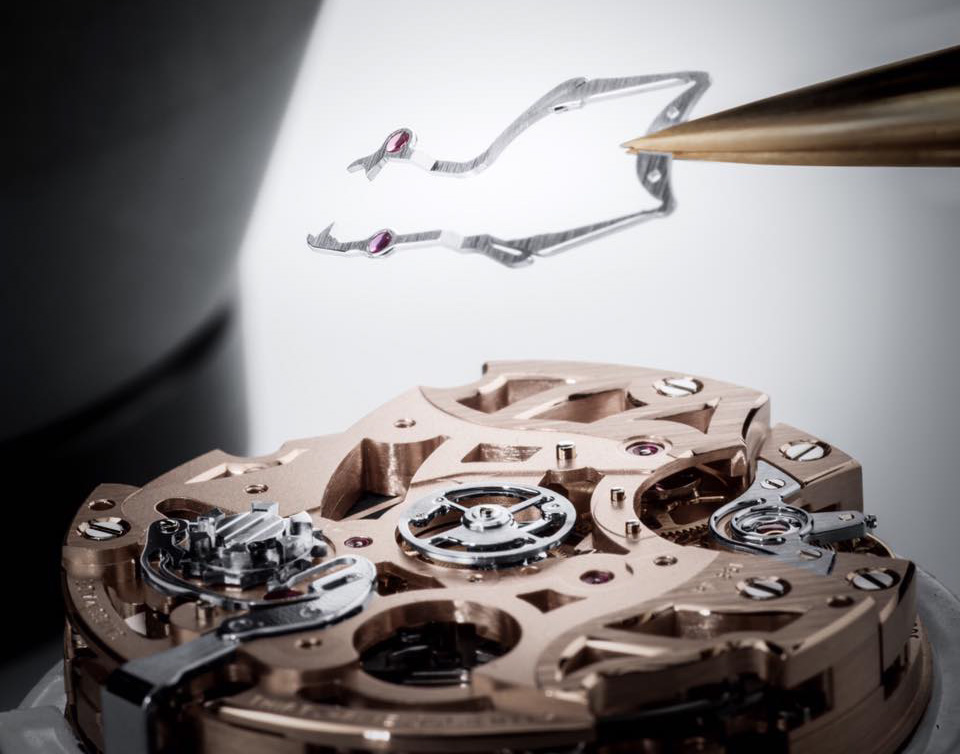
Parmigiani Fleurier Tonda Chronor использует гибкий зажим, который останавливает и освобождает колесо ратрапанте
Дилемма современного часового искусства - как быть актуальным в XXI веке и остаться верным вековым традициям? Для некоторых часовых домов ответ на этот вопрос заключается в том, чтобы внимательно следить за новыми технологиями, которые могут улучшить дизайн механических часов, не затрагивая их характер. В часах, как и в архитектуре, полезность является необходимой, но не единственной ценностью. В своей рекламе кварцевых часов 1970-х годов, «Seiko» была только наполовину права, сказав, что «все часы когда-нибудь будут сделаны именно так».
То, что происходит сегодня, это не столько энергетическая революция, сколько материальный драйв. Кремний, или, точнее, процесс CVD (химического парофазного осаждения), позволяет изготавливать мельчайшие компоненты с уровнем точности, намного превышающей возможности обычной механической обработки. Эти части могут быть просто напечатаны на кремниевой подложке, добавляя или удаляя материалы с помощью реактивных газов и плазмы. Что еще важнее, это стало катализатором для совершенно нового мышления.
В самом простом варианте, замена стандартных деталей их кремниевыми эквивалентами позволяет брендам предлагать часы, которые точнее измеряют время, служат дольше, и реже требуют сервиса, чем часы с обычными механизмами. А это - значительное достижение, учитывая, что послепродажное обслуживание является неотъемлемой частью бизнеса люксовых механических часов.
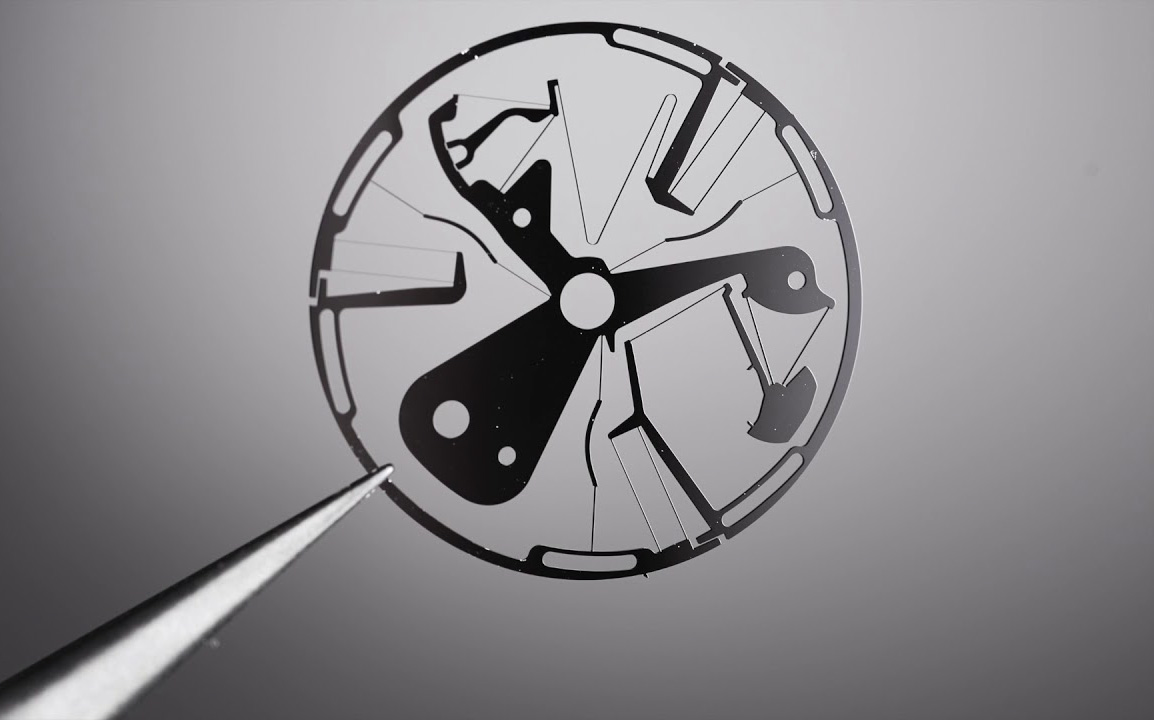
Кремниевый осциллятор, используемый в Zenith Defy Lab включает в себя все элементы анкерного спуска
Возьмите, к примеру, только что запущенный механизм «Baumatic» от «Baume & Mercier», который соответствует хронометрическим стандартам, и при этом имеет расширенную гарантию и увеличенные интервалы сервисного обслуживания. Это стало возможным почти полностью благодаря использованию кремния.
Теперь разработчики могут определять структуру компонента буквально по молекулам, проектируя детали, которые традиционно требовали сборки. В часовом производстве это означает уменьшение количества деталей: балансового колеса, пружины, спускового колеса, оси и анкера спускового механизма (обычно минимум 24 крошечных, труднообрабатываемых компонента) до четырех, трех или даже одной целой детали. Представьте себе создание ножниц из одной части вместо четырех.
Сравните это с механическими часами из традиционных материалов. Они имеют три проблемы: им нужна смазка, (которая со временем разлагается), их скорость может варьироваться в зависимости от температуры, и они должны быть защищены от магнитных полей. Кремний, с другой стороны, обладает низкими показателями трения, изотермическими и антимагнитными свойствами. Почти 20 лет назад это побудило швейцарский бренд «Ulysse Nardin» начать разработку кремниевых компонентов для своих часов, и привело к запуску коллекции «Freak» в 2001 году. «Freak» продемонстрировали потенциал кремния, и с тех пор технология, доказав свою надежность, постепенно внедряется во всей отрасли.
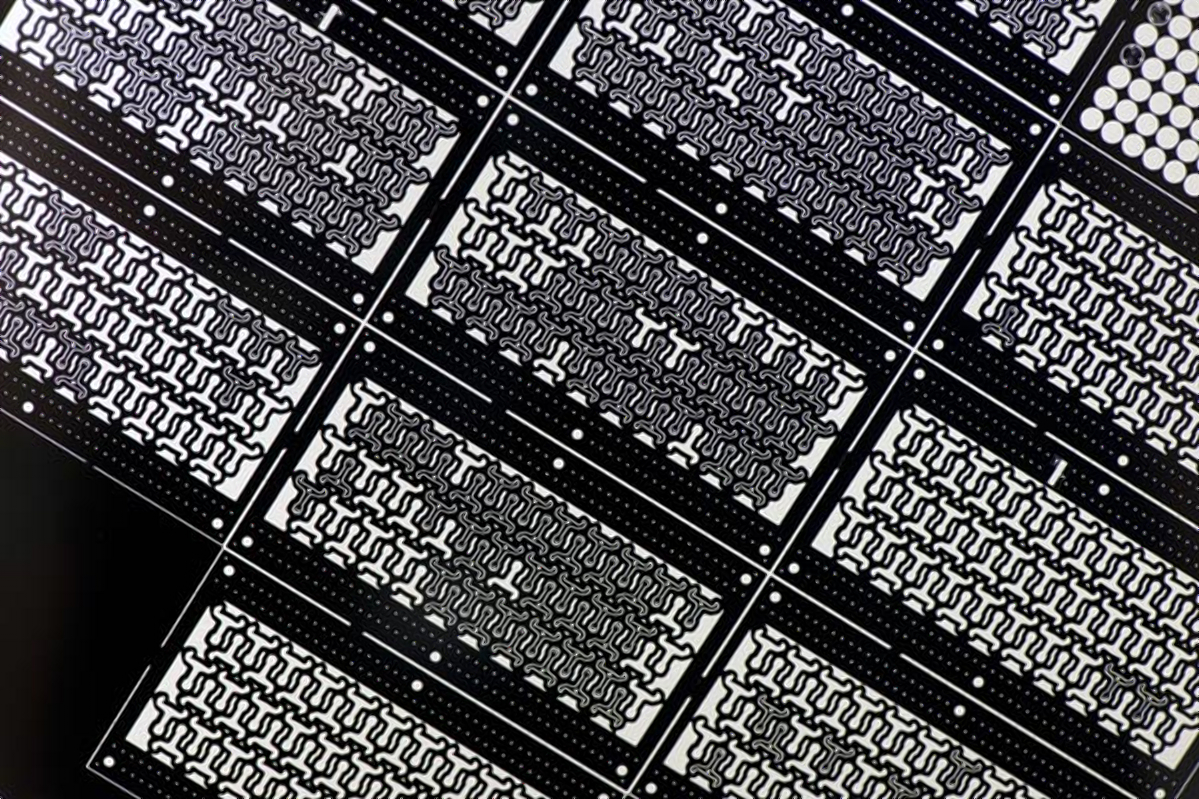
Пластина кремниевых анкеров Sigatec в производстве Ulysse Nardin
Другой пример, пружины. В большинстве механических швейцарских часов используются пружины, изготовленные из железо-никелевого сплава под названием «Nivarox», производимого одноименной компанией из металлической проволоки традиционным методом. Но господство «Nivarox» вскоре может подойти к концу.
Недавно исследователями из «Лаборатории механики материалов и наноструктур», входящей в состав «Empa» (Швейцарского федерального научно-исследовательского института материаловедения), разработана принципиально другая технология. И сегодня новая пружина уже проходит испытания у одного из швейцарских производителей.
Вместо традиционной навивки, команда «Empa» использовала гальванику для «выращивания» ходовых и волосковых пружин для часов. Процесс начинается с кремниевой пластины, аналогичной тем, которые используются для изготовления компьютерных чипов. Пластину покрывают электропроводящим слоем золота, поверх которого наносят слой светочувствительной краски. Затем свет проецируется на поверхность, и маска сохраняет проекцию в виде необходимой формы витой пружины. Освещенная область реагирует с краской, в результате чего она и золото под ней вытравливаются химикатами, оставляя на золоте только форму пружины. Затем пластина помещается в ванну, содержащую растворенные металлические соединения, в нее подается электрический ток, в результате чего металл осаждается на золотом контуре для создания пружины. Прежде чем пружина будет отправлена часовщику, требуется еще несколько дополнительных процессов проверки, очистки и обработки.
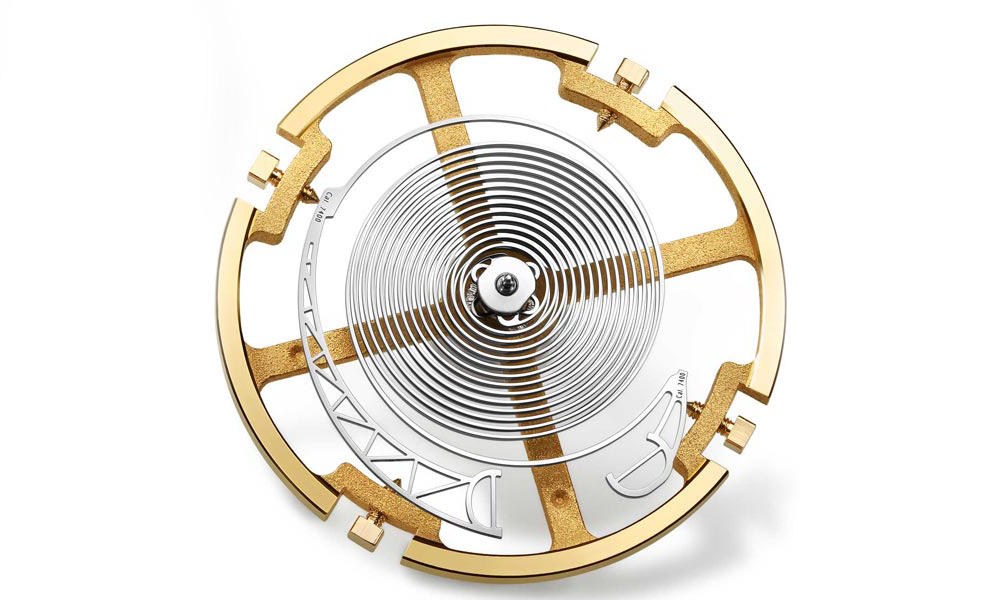
Кремниевая пружина с магнитной осью баланса Breguet в часах Classique Chronométrie 7727
Лаборатория также работает над вариациями процесса, включая 3D-печать, для изготовления пружин различной формы и для создания других микро-структур для механических часов. По словам Летиции Филипп, одной из исследователей «Empa», кое-что еще предстоит усовершенствовать, но этот процесс может создать новые типы пружин, которые открывают новые возможности дизайна для часовщиков.
«Материалы, которые используются в этом процессе, должны придать часовым пружинам большую устойчивость к температурам», - добавляет она. Кроме того, пружины можно сделать более легкими и, поскольку они наращиваются слой за слоем, то имеют определенные особенности структуры для различных типов часовых механизмов.
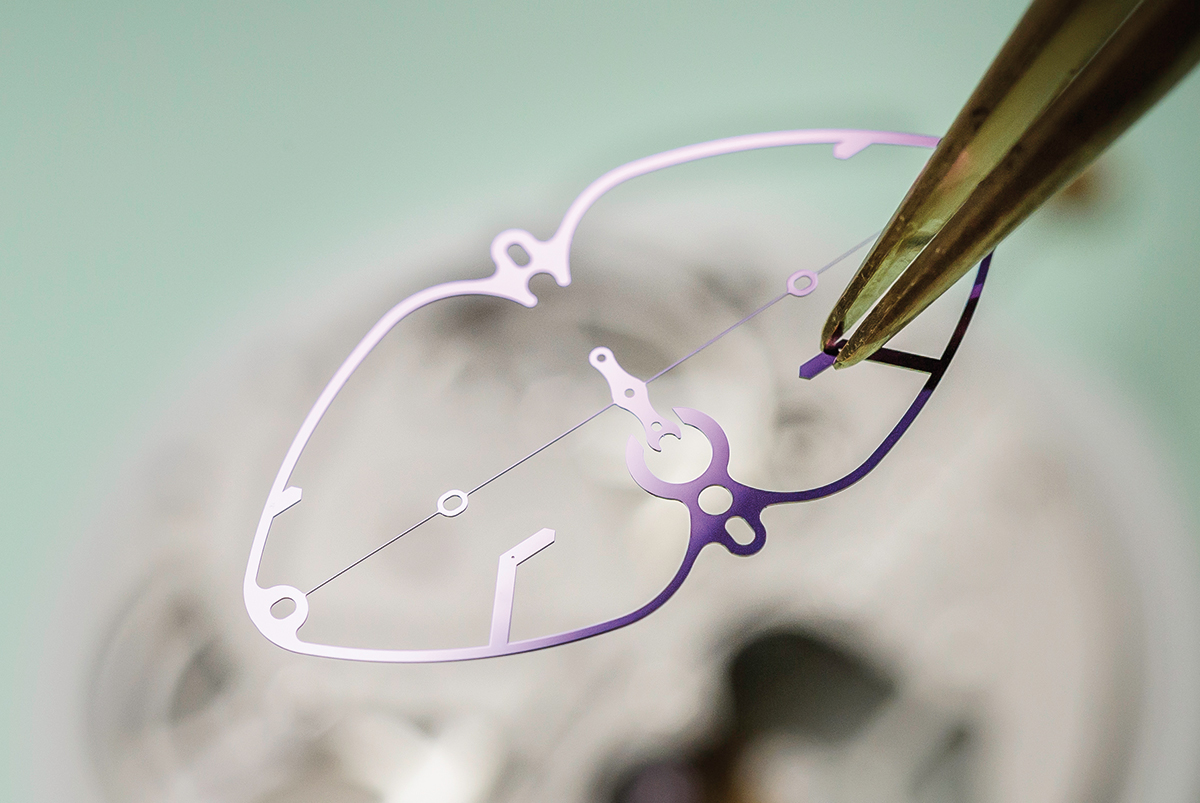
Girard-Perregaux спусковое лезвие толщиной 0,14 мм использовано в часах Constant Escapement LM
Разработчики часовых механизмов также быстро обнаружили, что процесс производства кремния позволяет им экспериментировать с геометрией, положив начало созданию невероятных форм, не поддающихся классификации. Так, новейшая спусковая система «Oscillomax» от «Patek Philippe» оснащена пружиной баланса, утолщенной на концах, что позволяет ей колебаться равномерно при любой ориентации.
Как показывает осциллятор «Girard-Perregaux Constant Force», эти компоненты могут очень отличаться от их традиционных эквивалентов. Он построен на основании тонкого лезвия, которое изгибается, поглощая энергию, а затем возвращается в исходное положение, обеспечивая точные импульсы механизму.
Выход «Zenith» на поле кремниевых компонентов - это детище Гая Симона, генерального директора «TAG Heuer», в партнерстве с «Делфтским техническим университетом», одним из ведущих исследовательских центров в этой области. Осциллятор «Zenith» представляет собой цельный кремниевый компонент без трения, который поддерживает постоянную частоту от полностью заведенного состояния часов до конца 60-часового запаса хода, что обычные часы могут только при наличии сложного механизма компенсации.
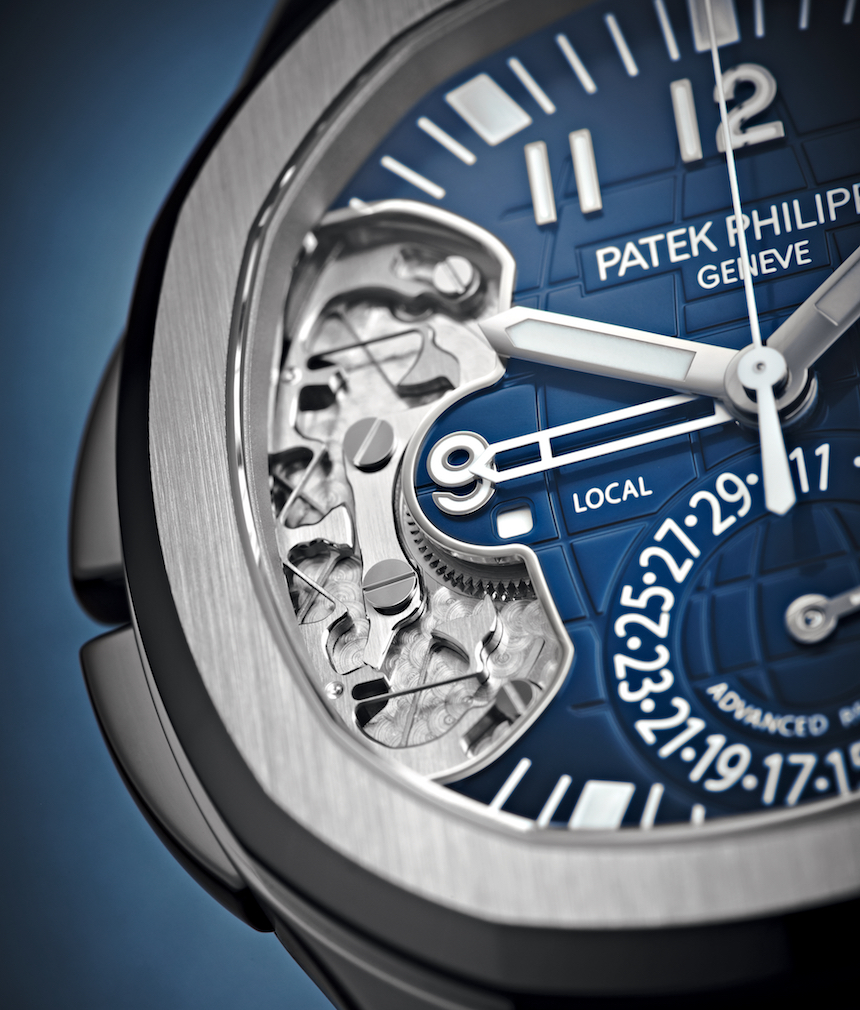
Patek Philippe Advanced Research Aquanaut Travel Time имеют стальной гибкий регулятор GMT
В отличие от угрозы, которую представляло для традиционной часовой индустрии изобретение кварца, в данном случае все наоборот. Известные бренды, как «Parmigiani Fleurier», «Omega», «Rolex» и «Patek Philippe», которые поддержали исследования в области использования кремния, взяли за основу новое мышление и применили его к более традиционным материалам, отдавая приоритет доказанной надежности перед новизной: так, калибр «Omega 8900» сочетает в себе оба подхода к производству часов. Он будет работать с большей точностью, чем традиционные часы, практически в любых условиях, с гораздо более длительным сроком обслуживания и гарантией.
Возможно, самая интересная позиция в этом вопросе - это позиция «Patek Philippe». Врожденно консервативная в своем подходе, исследовательская лаборатория компании «Advanced Research Team» должна уравновесить чистую полезность новых технологий с часовой культурой, на которой построен известный бренд. Но, как говорит Фредерик Майер, заместитель директора департамента: «Их может быть сложнее спроектировать и изготовить, но гибкие механизмы включают меньше деталей и в меньших размерах, что означает большую надежность».
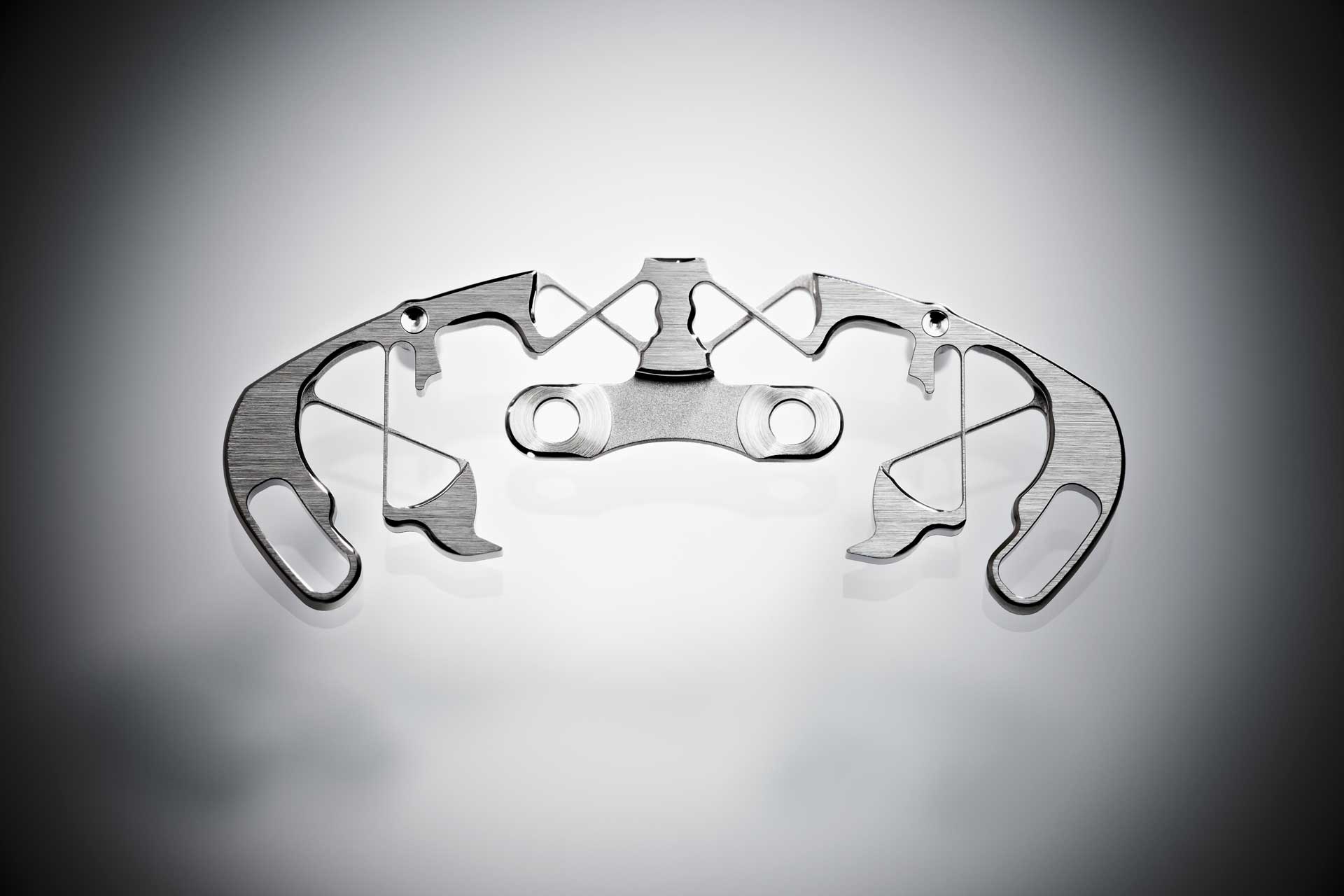
Гибкий стальной механизм Patek Philippe толщиной в 1.244 мм, использованный в часах Advanced Research Team
В прошлом году «Patek Philippe» продемонстрировал часы «Advanced Research Aquanaut Travel Time», оснащенные «совместимым» гибким механизмом, который регулирует индикацию GMT. Чтобы выполнять свою функцию, механизму необходимо передавать, хранить и изменять направление импульсов от кнопок - сложная задача, для которой обычно требуется узел из 30 или более компонентов, половина из которых требует смазки. Удивительно, но новый механизм включает всего 12 компонентов и сделан из стали с использованием как современных, так и традиционных технологий, с зазором в 150 микрон между скрещенными пружинами, что было бы невозможно представить еще несколько лет назад. Это просто демонстрация того, как технология может быть применена в будущем. Вы можете легко представить и более сложные сборки, однако, как добавляет Майер, «наша задача - сделать лучше «Patek Philippe», а не просто лучшие часы».